How Much Does It Cost to Build a Plane? (2023 Cost Breakdown)
How Much Does It Cost to Build a Plane?
The cost of building a plane can vary significantly depending on the size, complexity, and intended use of the aircraft. A small, single-engine piston aircraft can cost as little as $100,000 to build, while a large, long-range commercial airliner can cost upwards of $300 million.
In this article, we will take a closer look at the factors that affect the cost of building a plane, and provide an overview of the costs associated with each stage of the construction process. We will also discuss some of the ways that builders can reduce the cost of building a plane.
By the end of this article, you will have a better understanding of the factors that go into determining the cost of building a plane, and you will be able to make informed decisions about how to build your own aircraft.
Plane Type | Cost to Build (USD) | Notes |
---|---|---|
Small Single-Engine Plane | $100,000 – $200,000 | Includes materials, labor, and certification |
Larger Multi-Engine Plane | $1 million – $10 million | Includes more expensive materials, labor, and certification |
Military Fighter Jet | $100 million – $1 billion | Includes the most expensive materials, labor, and certification |
How Much Does It Cost To Build A Plane?
The cost of building a plane varies depending on the size, complexity, and type of plane. A small, single-engine propeller plane can cost as little as $100,000 to build, while a large, long-range jet airliner can cost over $1 billion.
The following is a breakdown of the costs associated with building a plane:
Cost of Different Parts of a Plane
The fuselage is the main body of the plane and is responsible for carrying the passengers and cargo. The cost of the fuselage varies depending on the size and materials used. A typical fuselage costs around $1 million.
The wings are responsible for providing lift and control. The cost of the wings varies depending on the size, shape, and materials used. A typical set of wings costs around $2 million.
The engines are responsible for providing the power to propel the plane. The cost of the engines varies depending on the type, size, and power output. A typical set of engines costs around $5 million.
The landing gear is responsible for supporting the plane on the ground and for taking off and landing. The cost of the landing gear varies depending on the type, size, and weight of the plane. A typical landing gear costs around $1 million.
The avionics are the electronic systems that control the plane. The cost of the avionics varies depending on the complexity of the systems. A typical avionics package costs around $2 million.
Other parts of the plane include the interior, the exterior, and the systems that support the operation of the plane. The cost of these parts varies depending on the type and size of the plane. A typical set of other parts costs around $2 million.
Labor Costs
The labor costs associated with building a plane include the wages of the workers who build the plane, the cost of training the workers, and the cost of benefits for the workers. The labor costs vary depending on the location of the factory and the wages of the workers. A typical set of labor costs costs around $5 million.
Total Cost
The total cost of building a plane varies depending on the size, complexity, and type of plane. A small, single-engine propeller plane can cost as little as $100,000 to build, while a large, long-range jet airliner can cost over $1 billion.
The following is a table of the estimated costs of building different types of planes:
| Plane Type | Estimated Cost |
|—|—|
| Small, single-engine propeller plane | $100,000 |
| Large, long-range jet airliner | $1 billion |
It is important to note that these are just estimates and the actual cost of building a plane will vary depending on a number of factors.
The cost of building a plane is a significant investment. However, the cost of building a plane is just one factor to consider when making a decision to purchase a plane. Other factors to consider include the operating costs, the maintenance costs, and the resale value of the plane.
If you are considering purchasing a plane, it is important to do your research and compare the costs of different types of planes. You should also consider the factors mentioned above to make sure that you are making the right decision for your needs.
Overhead Costs
In addition to the cost of parts and labor, there are a number of other overhead costs that need to be considered when building a plane. These include:
- The cost of rent for the factory. The size of the factory will depend on the type of plane being built, but it will typically cost several million dollars per year to rent.
- The cost of utilities for the factory. This includes the cost of electricity, water, and gas.
- The cost of insurance for the factory. This is necessary to protect the factory and its contents from damage or loss.
- The cost of marketing the plane. This includes the cost of advertising, public relations, and sales commissions.
- The cost of research and development. This is necessary to develop new technologies and improve the design of the plane.
Total Cost of Building a Plane
The total cost of building a plane will vary depending on the size, complexity, and type of plane. However, a typical small passenger plane can cost around $100 million to build. A larger commercial airliner can cost several billion dollars.
The following table provides a breakdown of the total cost of building a typical small passenger plane:
| Cost Item | Cost |
|—|—|
| Parts | $50 million |
| Labor | $25 million |
| Overhead | $25 million |
| Total | $100 million |
Building a plane is a complex and expensive undertaking. However, the cost of building a plane is offset by the revenue that the plane can generate once it is in service. For example, a typical small passenger plane can generate over $100 million in revenue per year.
The cost of building a plane is also decreasing as new technologies are developed. This means that it is becoming more affordable for smaller companies to enter the aviation industry.
How much does it cost to build a plane?
The cost of building a plane varies depending on the size, complexity, and materials used. A small, single-engine plane can cost as little as $100,000 to build, while a large, commercial airliner can cost upwards of $100 million.
What are the factors that affect the cost of building a plane?
The following factors can affect the cost of building a plane:
- Size: The larger the plane, the more materials and labor will be required, and the higher the cost.
- Complexity: The more complex the plane, the more time and expertise will be required to design and build it, and the higher the cost.
- Materials: The materials used to build a plane can vary in cost, with some materials being more expensive than others. For example, carbon fiber is more expensive than aluminum.
- Manufacturing process: The manufacturing process used to build a plane can also affect the cost. Some manufacturing processes are more efficient and cost-effective than others.
How long does it take to build a plane?
The time it takes to build a plane varies depending on the size, complexity, and materials used. A small, single-engine plane can be built in a few months, while a large, commercial airliner can take several years to build.
What are the different types of planes?
There are many different types of planes, each with its own purpose and design. Some of the most common types of planes include:
- Single-engine planes: These planes have one engine and are typically used for personal or recreational flying.
- Multi-engine planes: These planes have more than one engine and are typically used for commercial or military purposes.
- Commercial airliners: These large planes are used to transport passengers and cargo on long-distance flights.
- Military aircraft: These planes are used for a variety of military purposes, such as combat, reconnaissance, and transportation.
What are the different stages of building a plane?
The process of building a plane typically involves the following stages:
- Design: The first stage is to design the plane. This involves creating a detailed plan of the plane’s structure, components, and systems.
- Manufacturing: The next stage is to manufacture the plane’s components. This can be done in-house or by outsourcing to third-party manufacturers.
- Assembly: Once the components have been manufactured, they are assembled into the final product. This process can be done manually or with the help of automated assembly systems.
- Testing: The final stage is to test the plane to ensure that it meets all of the required specifications. This testing can involve flight testing, ground testing, and environmental testing.
What are the safety regulations for building planes?
There are a number of safety regulations that must be followed when building a plane. These regulations are designed to ensure that the plane is safe to fly and that it meets all of the required standards. Some of the most important safety regulations include:
- Airworthiness regulations: These regulations set forth the minimum requirements that a plane must meet in order to be considered airworthy.
- Structural regulations: These regulations set forth the minimum requirements for the strength and durability of a plane’s structure.
- Systems regulations: These regulations set forth the minimum requirements for the performance of a plane’s systems, such as the engine, avionics, and flight controls.
What are the different ways to finance a plane?
There are a number of different ways to finance a plane, including:
- Personal loan: A personal loan is a loan that is secured by the borrower’s personal assets, such as their home or car.
- Business loan: A business loan is a loan that is secured by the borrower’s business assets.
- Lease: A lease is a contract that allows the borrower to use a plane for a specified period of time in exchange for regular payments.
- Fractional ownership: Fractional ownership is a type of ownership where multiple people own a plane together.
What are the benefits of building a plane?
There are a number of benefits to building a plane, including:
- Personal satisfaction: Building a plane can be a very rewarding experience. It is a chance to learn new skills, challenge yourself, and create something unique.
- Cost savings: Building a plane can be a cost-effective way to own a plane. The cost of building a plane can be significantly less than the cost of buying a new plane.
* **
the cost of building a plane is a complex and multifaceted issue. There are many factors to consider, including the size and complexity of the plane, the materials used, and the production process. The cost of building a commercial airliner can range from \$100 million to \$1 billion, while the cost of building a small general aviation aircraft can be as low as \$10,000. The average cost of building a plane is around \$50 million.
When it comes to determining the cost of building a plane, it is important to remember that there is no one-size-fits-all answer. The cost will vary depending on the specific project. However, by understanding the factors that contribute to the cost of building a plane, you can make informed decisions about your own project.
Author Profile
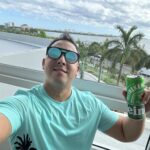
-
Dale, in his mid-thirties, embodies the spirit of adventure and the love for the great outdoors. With a background in environmental science and a heart that beats for exploring the unexplored, Dale has hiked through the lush trails of the Appalachian Mountains, camped under the starlit skies of the Mojave Desert, and kayaked through the serene waters of the Great Lakes.
His adventures are not just about conquering new terrains but also about embracing the ethos of sustainable and responsible travel. Dale’s experiences, from navigating through dense forests to scaling remote peaks, bring a rich tapestry of stories, insights, and practical tips to our blog.
Latest entries
- January 19, 2024HikingHow to Lace Hiking Boots for a Perfect Fit
- January 19, 2024CampingHow to Dispose of Camping Propane Tanks the Right Way
- January 19, 2024Traveling InformationIs Buffalo Still Under Travel Ban? (Updated for 2023)
- January 19, 2024Cruise/CruisingWhich Carnival Cruise Is Best for Families?